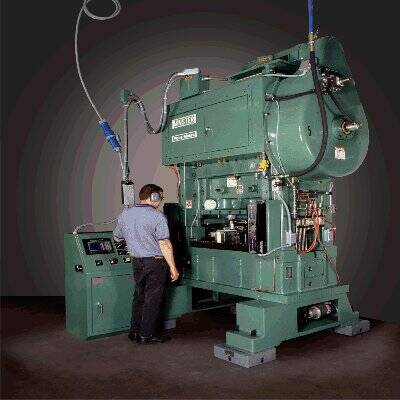
In order to understand 5-S I'd like you to imagine that you have just been hired to a new company and are responsible for tightening two 1-inch bolts, two 1/2-inch bolts, and two 3/8-inch bolts on 10 pieces of identical machinery once an hour. On your first day on the job you are given your trusty toolbox, shown the location of the machines, the location of the bolts on the machines and told that while you're tightening the bolts on each machine it will be shut down and its production will have to stop.
Your new supervisor tells you that every moment these machines are down the company is losing money and falling behind.
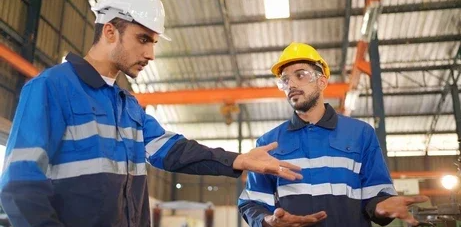
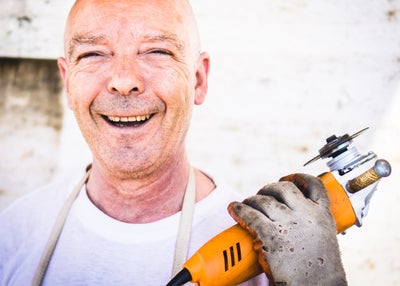
A friendly coworker tells you that the supervisor loses his temper and yells at people when things aren't getting done fast enough. He doesn't want to hear any excuses or any suggestions. Finally, he tells you that the turnover rate for your job has been high and that nobody lasts more than 6 months. "They just get burned out and quit."
Uh-oh! Hurry up the first machine is off you've got to tighten those bolts!
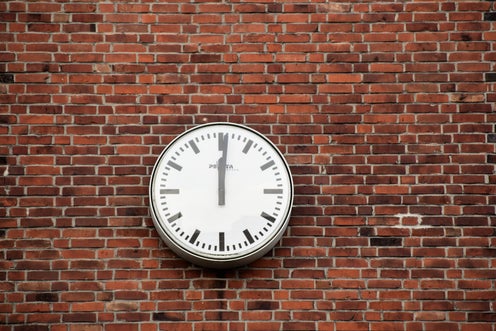
You hurry to the first machine as quickly as you can...open your toolbox and...
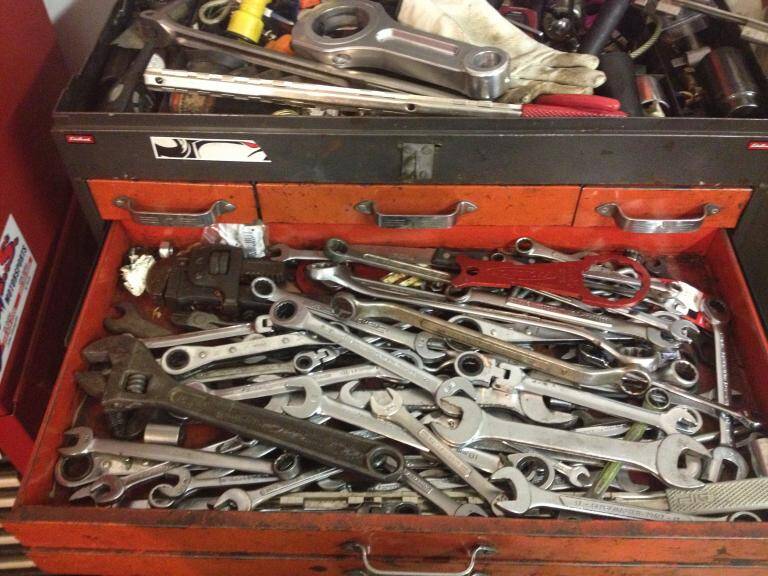
At this point ask yourself two questions. First, how long is it going to take you to find the correct wrenches in that mess. Second, if you had to deal with this every day how long would it take you to "burn out" and quit?
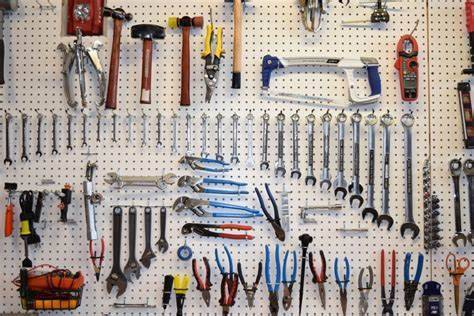
5-S is alliterative description of a process of organizing your workspace to maximize efficiency, reduce downtime, and improve cognitive ergonomics for workers. The five individual S are
Sort- This step involves sorting through all items and tools in the workplace to separate essential items from non-essential ones.
Set in order- This step is to arrange the essential items in a systematic and logical order. Tools and equipment should be placed in designated locations, making them easy to find and use when needed.
Shine- This step focuses on maintaining cleanliness and tidiness in the workplace. Regular cleaning and inspection of tools and equipment are essential to prevent dirt, dust, and debris from causing defects or accidents.
Standardize- Once the workplace is organized and cleaned, we set this as the new standard of how we do business.
Sustain- Finally, this step involves creating a culture of continuous improvement and discipline. All team members are held accountable by management and their coworkers to maintain the standard.
The short video below takes you through a brief game to show you firsthand the benefits of applying the 5-S principles.
Now that we have seen the problem-solving capabilities of 5-S and have a basic understanding I wanted to close with an underlying problem that I touched on in the scenario at the beginning of this page. Often times we hear industrial workers use phrases like "burned out", "need a vacation", or even complain about extreme mental fatigue at the end of their day. We also hear phrases like "zoned out", "complacency", and "distracted" during mishap investigations. The feeling you got in the beginning of the video where you were anxiously searching for numbers as fast as you could applied across an eight-hour day is exhausting. The implementation of the processes we just examined have been linked to improved cognitive ergonomics, reduced stress related injuries, and a higher level of job satisfaction.