Understanding and maintaining the balance of the individual vectors that shape business efficiency is critical to ensuring profitability.
- Income
- Expenses
- Production
- Profit
- Profitability
- Efficiency of human and physical capital
While an improvement of all vectors would be ideal some vectors such as income are more difficult, expensive, and time consuming to improve than others. Ultimately focusing on the easier to influence vectors expenses, production, and efficiency will deliver the fastest and most impressive results.
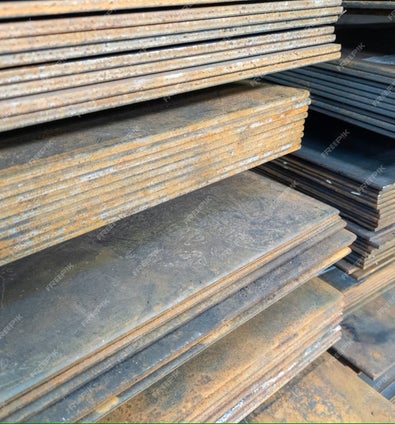
Production:
Overproduction of goods carries the same expenses as storing excess material. While storing a surplus of completed goods reduces the lead time to fill orders it also results in having to store products that could become damaged, lost, or obsolete.
Defects damage business efficiency in multiple ways from returned goods to quality reputation. Although different industries have maintained an acceptable defect rate with new advances in AI technology, precision machines, and feedback sensors there is a new push to move from an acceptable DPMO or SIGMA level to zero defect manufacturing. Currently zero defect manufacturing or ZDM is being used in critical applications such as missile systems where the effects of a failure could be catastrophic.
Expenses:
While every business has necessary operating expenses eliminating unnecessary expenses. One of my first process improvement projects involved an industrial manufacturer who had recently moved to a larger facility and maintained an off-site storage yard for steel plates used in fabrication. This manufacturer expended 500 sheets of metal of varying thickness per month. In the first hour of being at the facility it was determined that they had over 16,000 sheets of metal stored in the facility, at the storage yard, and leaning behind their manufacturing facility. When asked why they had so much excess steel the answer was that they received a 5% discount on orders over 100 sheets. So what was the unnecessary expense? The steel plates were still an asset that the company possessed, and they had saved 5% over 160 full price transactions. For each sheet of steel there were three unnecessary expenses.
- The expense of storing the materials
- The cost of transporting materials from storage to the facility
- The cost of materials destroyed by the weather from being stored outside
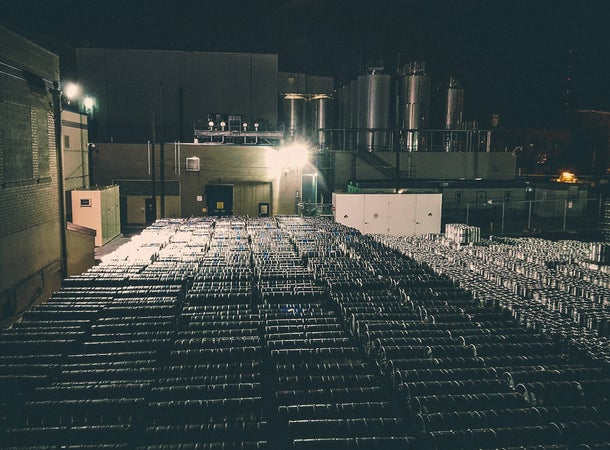
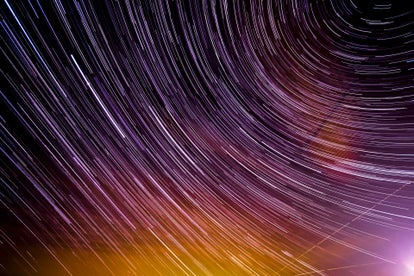
Efficiency:
Inefficient use of personnel and or equipment causes excess cost, delays in production, and potentially impacts deadlines. As described on the Six Sigma page time spent waiting is one of the most common wastes. Excessive tooling changes, ineffective shift scheduling, and ineffective order of operations are the most common offenders in a manufacturing enviornment.
The most cost-effective way to resolve issues with these vectors or make improvements to profit based on them is to employ a consultant to implement a Process Improvement Plan such as Six Sigma, Lean Manufacturing, and a 5-S organization plan.